Piece-rate pay: what it is, pros, cons, and how to calculate it
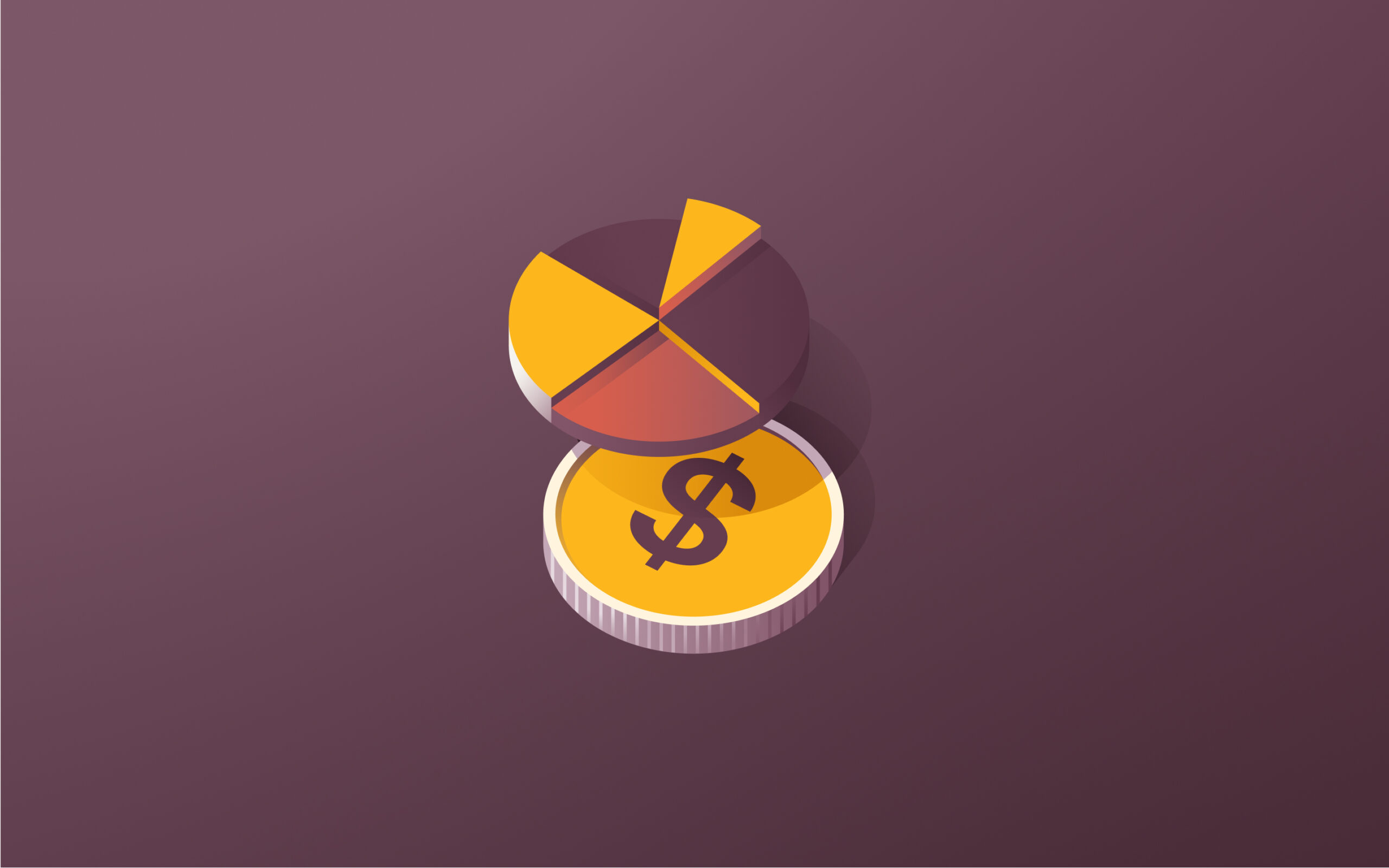
While piece-rate pay has long been a common compensation structure in industries like agriculture and manufacturing, it’s less well-known in other contexts. As more businesses explore flexible, performance-based compensation, piecework, sometimes known as “per project” or “per unit” pay, has started to gain traction in fields dominated by freelancing and gig work.
In this article, we’ll go over the ins and outs of piece-rate pay systems, from the formulas you use to calculate worker compensation to the best-fit business structures.
What is piece-rate pay and how does it work?
Piece rate pay, sometimes known as piece work pay, compensates employees based on units of work completed during working hours versus the number of hours worked or a fixed salary.
Example: Widgets.io pays senior technicians $100 per widget built. Morgan, who has ten years of experience in the widget field, completes ten widgets in an eight-hour shift for a total compensation of $1,000. Alex, who was just promoted to senior technician, completes seven widgets during the same shift and earns $700.
The Fair Labor Standards Act (FLSA) offers pieceworkers the same protections as other non-exempt employees: workers paid under a piecework system must receive compensation equal to the applicable minimum wage and can claim overtime pay if they work over 40 hours per week. If a worker’s total pay fails to meet minimum wage requirements, the employer must make up the difference.
Example: Greenies pays landscaping assistants $15 per lawn mowed. In one 40-hour work week, Taylor mows 15 lawns and earns $225. Under the FLSA, Taylor’s compensation must equal $7.25 an hour or $290 per week. Taylor’s employer adds $65 to their weekly check to ensure federal minimum wage laws compliance.
Businesses that commonly use piece-rate pay
Piecework pay works well in industries with easy-to-measure, repeatable tasks that lead to specific outputs, like manufacturing. Businesses that rely on highly-skilled workers, such as machine repair, can also leverage a piece-rate pay system to incentivize productivity by aligning their interests with business goals.
Industries where piece-rate pay can be a good fit include:
- Manufacturing
- Automotive repair
- Construction
- Content creation
Piece-rate vs. time rate: key differences
While time-rate systems compensate workers based on how long they work, piece-rate systems pay employees according to how much they produce. In a piece-rate system, businesses incentivize teams to complete tasks as efficiently as possible by tying compensation directly to productivity. On the other hand, a time-rate system gives workers the freedom to take their time completing a task to the absolute best of their abilities.
Depending on their financial goals and personalities, employees may see more benefits in piece-rate or time-rate pay. Someone who needs minimal supervision to be productive and enjoys the challenge of working ‘against the clock’ may appreciate the earning potential of piecework pay. If an employee needs more income stability than minimum wage provides, however, a time-rate system with fixed hours might hold more appeal. And for those who prefer to take their time, a piece-rate system’s focus on speed might feel more like pressure than motivation.
3 types of piece-rate systems
Piece-rate systems typically operate in one of three different structures. The best choice for a business depends on a few factors, but most focus on achieving the right balance between quantity and quality of worker output while maintaining compliance with wage and hour requirements.
1. Straight piece-rate system
In a straight piece-rate system, employees are paid a fixed amount for each unit of work performed, regardless of how long it takes to complete the job. This straightforward model works well in settings like factories and is a common form of piecework.
Example: Casey works on a manufacturing line in a widget factory and earns $5 for every widget produced. In an eight-hour shift, Casey completes 200 widgets and earns $1,000.
2. Differential piece-rate system
A differential piece-rate system applies increasing pay rates to work units, incentivizing higher productivity levels. Workers are paid one rate up to a specific production threshold and a higher rate for exceeding it.
Example: Casey finds a new job at a different widget factory. The company pays $5 per widget, up to 100 widgets, and then $6 for any additional widgets. In an eight-hour shift, Casey completes 200 widgets and earns $1,100.
3. Hourly pay and piece-rate system
An hourly pay and piece-rate system combines elements of both a time-based and a production-based model. Employees receive base compensation as an hourly wage, but can earn more on a per-piece basis by exceeding production targets for a pay period.
Example: Now an experienced builder of widgets, Casey migrates to a factory that operates on a hybrid of hourly pay and a piece-rate system. Casey earns a base rate of $100 per hour plus an additional $5.00 for any widgets above 100. For an eight-hour shift that results in 200 widgets, Casey gets paid $1,300.
When to apply piece-rate pay?
A piece-rate system works well in settings where workers perform repetitive tasks and need minimal supervision. It also lends itself to industries with clear, easily measured outputs. Applying a piece rate pay system can also minimize the complexity of tracking performance and allow for a straightforward evaluation of outputs.
1. When the tasks are repetitive
Piece rate work works well when employees perform consistent, repetitive tasks. Assembly line workers in an electronics factory, for example, may focus on soldering the same components together for each product. Piece rate pay incentives them to complete each unit as efficiently as possible.
2. When the business is interested in quality
Businesses that need to guarantee a minimum standard of uniformity can attach quality-based incentives to motivate workers to complete tasks quickly and precisely. A clothing manufacturer might reward tailors or seamstresses with a bonus for completing a certain number of garments that pass all quality checks.
3. When the business is interested in quantity
In a seasonal industry like agriculture, employers need to optimize workforce productivity within a limited time frame. A farmer might pay field workers a piece rate per basket of fruit picked to motivate workers to move as quickly as possible and reduce the risk of crops rotting on the vine.
Pros of piece-rate pay
For businesses with easy-to-quantify outputs, a piece-rate system can help incentivize workers by connecting earnings directly to productivity. The more units produced or services completed, the larger the employee’s paycheck. In industries where output directly correlates with revenue, such as manufacturing, businesses can more easily predict labor costs by looking at past production data.
Higher production rates
When working faster means more money, employees have a good reason to work as productively as possible. A factory that operates on the basis of piece-rate compensation sends a clear message to its workforce that boosting production also benefits their bank accounts.
Easier wage calculation
Piece rate compensation can simplify the process of computing employee compensation. For example, a shipping company can easily calculate how much a worker earns during a shift by multiplying the number of boxes delivered by the rate of payment per shipment.
Increased employee control over compensation
A piece-rate system allows employees to decide how much effort to exert based on their financial needs at a given point in time. For example, a freelance designer paid per post can plan to work overtime for three months to accumulate savings before slowing down for a month while traveling.
Cost control
For businesses with consistent production volumes, a piece rate system can help predict and manage labor costs. A tutoring service that pays each teacher per lesson can forecast labor costs by multiplying the per-lesson rate by the average number of tutoring sessions booked each semester.
Cons of piece-rate pay
While piece rate pay can drive employees to be more productive, it can also lead them to cut corners or go too far above and beyond. Businesses considering piece-rate pay systems should carefully consider their targets and support employees with proper equipment, adequate rest, and clear institutional processes.
Pressure on employees
Employees working against ambitious production quotas may experience physical and emotional burnout. Businesses considering piece-rate pay as a tool to boost productivity should take steps to ensure workers have adequate time to rest and recharge without sacrificing wages.
Quality deterioration
A hyper-focus on quantity can lead to workers sacrificing time and attention needed to ensure quality. Writers paid by the article, for example, may speed through research and editing in an effort to complete as many assignments as necessary to meet their income goals.
Compliance issues
Ensuring compliance with minimum wage and overtime laws isn’t always straightforward under a piece-rate compensation system. A ride-hailing company calculating total pay for drivers needs to consider not only base pay but also wait times and tips for each fare.
Non-optimized processes
Without proper tools and clear quality standards, a piece-rate system can amplify process inefficiencies instead of enhancing productivity. Creators for a digital marketing agency struggling against a long approval process or outdated scheduling tools may feel obliged to compromise on quality to comply with the content plan.
How to calculate piece-rate pay
How a business calculates piece-rate pay depends on the specific payment structure. Below, we’ll review the formulas associated with different types of piece-rate compensation before walking through examples of each.
“Flat Rate” per piece
In a “flat rate” per piece setup, employees are paid a fixed amount per unit produced or task completed.
Paycheck amount = Pieces or tasks x Rate
“Flat Amount” per group of pieces
Businesses using a “flat amount” formula pay employees a flat rate per group of units or tasks.
“Wages + Piece Rate”
A “wages plus piece rate” system offers employees a base hourly compensation plus a piece-rate incentive for every unit produced or task completed.
Paycheck amount = (Hourly rate x Hours worked) + (Pieces or tasks x Rate)
3 piece-rate pay examples
Now that we understand the logic behind each formula, let’s see how businesses might apply them to different types of piece work.
Flat piece-rate pay
Kai works at a bakery and earns $2 for every loaf. In one 40-hour work week, Kai bakes a total of 500 loaves.
Paycheck amount = Pieces or tasks x Rate
Paycheck amount = 500 loaves x $2 per loaf
Paycheck amount = $1,000
To double-check compliance with the state’s minimum wage law, the bakery divides Kai’s total paycheck by the number of hours worked. Kai earned the equivalent of $40 per hour, well above the federal minimum wage of $7.25 per hour.
“Flat amount” per group of pieces
Ari works in a warehouse sorting packages. The company pays $50 for every 20 packages sorted. In one 12-hour shift, Ari sorts 120 packages.
Paycheck amount = (Pieces or tasks / Number in group) x Rate
Paycheck amount = (120 / 20) x $50
Paycheck amount = 6 x $50
Paycheck amount = $300
“Wages + Piece Rate”
Riley works on the assembly line in a plastics plant and earns $15 per hour, plus $3 for every piece molded. Riley clocks in for 40 hours in a standard workweek and molds 100 pieces.
Paycheck amount = (Hourly rate x Hours worked) + (Pieces or tasks x Rate)
Paycheck amount = ($15 x 40) + (100 x $3)
Paycheck amount = ($600) + ($300)
Paycheck amount = $900
The next week, Riley picks up an extra shift and works an additional 12 hours at a rate of time and a half. For Riley’s next paycheck, the factory needs to account for this overtime and the 20 extra pieces Riley molded.
Paycheck amount = (Hourly rate x Hours worked) + (Pieces or tasks x Rate) + (Overtime rate x Overtime Hours)
Paycheck amount = ($15 x 40) + (120 x $3) + ($22.50 x 12)
Paycheck amount = ($600) + ($360) + ($270)
Paycheck amount = ($600) + ($360) + ($270)
Paycheck amount = $1,230
Paycheck amount = (Pieces or tasks / Number in group) x Rate
Compliance considerations on piece-rate pay
The complexities of piece-rate pay systems can lead to extra compliance considerations, particularly when it comes to minimum wage laws. Because it’s the business that bears the cost when an employee falls short, it’s important to have tools and systems in place to track time and attendance and calculate payroll to ensure you stay on the right side of the law.
1. Piece-rate pay and minimum wage
Employees paid under a piece-rate pay system still benefit from the minimum hourly wage protections of the FLSA and state wage and hour laws. Employers whose workers don’t reach that compensation threshold will need to make up the difference.
If you plan to pay your workers with piece-rate compensation, you’ll need to convert their total pay into an hourly rate.
- Step 1. Calculate the worker’s total compensation by multiplying the number of units or tasks completed by the piece rates.
- Step 2. Divide the worker’s total compensation by the number of hours worked.
- Step 3. Compare the worker’s “hourly rate” to federal and state minimum wage requirements.
2. Piece-rate pay and overtime
When piece-rate workers work more than 40 hours per week, they’re entitled to receive overtime pay for pieces completed outside standard working hours. While you have the option to calculate overtime based on the number of pieces produced during standard and extra hours, many businesses prefer to convert the employee’s compensation to an hourly rate and then calculate the time-and-a-half rate.
- Step 1. Calculate the worker’s standard pay by multiplying the number of units produced during regular hours by the standard piece rate.
- Step 2. Divide the total regular pay by the total number of hours worked to find the hourly base rate.
- Step 3. Multiply the hourly base rate by .05 to find the half-time rate.
- Step 4. Multiply the half-time rate by the number of overtime hours worked and add the total regular pay to find the worker’s total compensation.
3. Piece-rate pay and non-productive periods
Employers must compensate their piece-rate workers for time spent in meetings or training and even breaks. Some states, such as California, require that employers track these hours separately and pay compensation equal to at least the federal minimum wage.
Streamline compensation and stay compliant with Rippling
Using natively built payroll software, Rippling's payroll software offers a seamless data pipeline that consolidates all your payroll functions on a single platform for a globally compliant pay run. Combined with Rippling’s suite of benefits administration and time and attendance tools, it streamlines the entire payroll process.
With Rippling, you can:
- Manage time and attendance natively
- Run unlimited off-cycle pay runs at no extra cost
- Set up multiple pay schedules, pay rates, and pay types in just a few clicks
- Automatically calculate prorated pay runs for new or promoted employees
- Automatically calculate overtime for every country
- Make changes after submitting payroll
FAQs on piece-rate pay
What are the legal risks of using piece-rate pay?
Legal risks of using piece rate pay include failure to meet applicable minimum wage requirements, miscalculating overtime pay, and failing to pay employees for non-productive work time. These errors can negatively impact workers’ net pay and lead to labor disputes.
Can piece-rate pay include different rates for different tasks?
Yes, piece-rate pay can include different rates for different tasks. More complex or multi-step duties may be compensated at a higher rate than simpler tasks. Applying different rates to different types of tasks can complicate the payroll process, however.
What records should employers keep for piece-rate workers?
Employers should plan to keep the same records for piece-rate workers as they do for hourly or salaried employees. In particular, employers using a piece-work system will want to retain records of the total number of hours worked, overtime pay and calculations, and piece rates applied to specific tasks.
Run payroll right every time
This blog is based on information available to Rippling as of December 12, 2024.
Disclaimer: Rippling and its affiliates do not provide tax, accounting, or legal advice. This material has been prepared for informational purposes only, and is not intended to provide or be relied on for tax, accounting, or legal advice. You should consult your own tax, accounting, and legal advisors before engaging in any related activities or transactions.